The barrel is an important part of the
Extruder screw barrel in the extrusion compression molding system. The barrel and the screw work together, the barrel accommodates the screw, and the screw rotates in the barrel. When the screw rotates and pushes the plastic to move forward in the barrel, the outside of the barrel heats and conducts heat to the plastic in the barrel, and the volume of the thread on the screw gradually shrinks, so that the plastic in the thread groove is squeezed, turned over and sheared. After the action of various forces such as cutting, it is uniformly mixed and plasticized. As it moves to the front of the barrel, it gradually melts into a viscous flow state, completing the plasticization of the plastic. The normal cooperation between the barrel and the screw ensures the continuous extrusion of raw materials for the extruder.
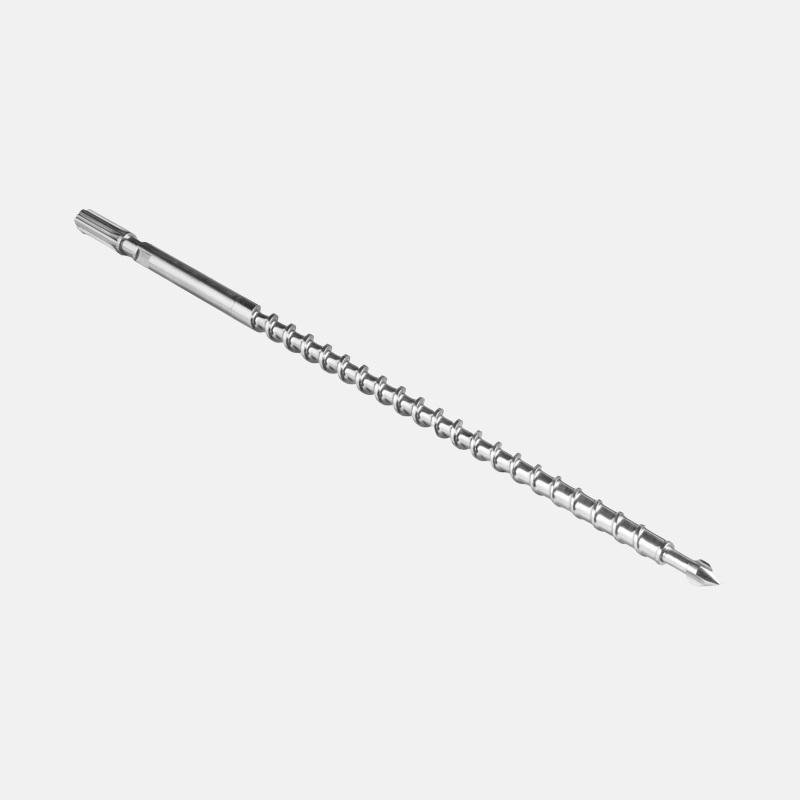
Common barrel structures are integral, segmented, bushing and bimetallic.
(1) Integral structure barrel: Integral structure barrels are widely used in extruders, especially when the extruder specifications are small, integral barrels are generally used. The arrangement of the heating and cooling devices of the barrel is convenient, the temperature control is easy to ensure, and the machining accuracy of the barrel is high.
(2) Segmented structure barrel: The segmented structure barrel is mainly used in larger size extruders and vented extruders. Because the barrel is divided into several sections, the length of each section of the barrel is small, which brings convenience to machining; however, the inner diameter and concentricity accuracy of several sections of the barrel are difficult to achieve uniform; The barrel is connected with flanges, which brings certain difficulties to the arrangement of the heating and cooling devices of the barrel, and the temperature control of heating and cooling will not be too uniform.
(3) Bushing or casting wear-resistant alloy on the inner diameter of the barrel: In order to save precious alloy steel, the barrel of the larger extruder is usually formed by cast steel, and then a wear-resistant alloy bushing or a wear-resistant alloy bushing is added after finishing the inner hole. Cast a layer of wear-resistant alloy material.
(4) The application of bushing barrels or casting a layer of wear-resistant alloy barrels in large extruders not only saves a lot of precious alloy steel and reduces equipment manufacturing costs, but also creates opportunities for future barrel maintenance. Convenient conditions: when the barrel alloy bushing is seriously worn, the barrel can work normally as long as the bushing is replaced, saving equipment maintenance time.