Cause of wear:
1. Each plastic has an ideal plasticizing processing temperature range, and the processing temperature of the barrel should be controlled to make it close to this temperature range. When the granular plastic enters the
Parallel twin screw barrel from the hopper, it will first reach the feeding section, and there will inevitably be permanent friction in the feeding section. When these plastics are not heated enough and melt unevenly, it is easy to cause increased wear on the inner wall of the barrel and the surface of the screw. Similarly, in the compression section and homogenization section, if the molten state of the plastic is disordered and uneven, it will also cause faster wear.
2. The speed should be adjusted properly. Because some plastics are added with reinforcements, such as glass fiber, minerals or other fillers. These substances tend to be much more abrasive to metallic materials than molten plastic. When injecting these plastics, if they are molded at a high speed, while increasing the shear force on the plastic, it will also make the reinforcement correspondingly produce more shredded fibers. The shredded fibers contain sharp ends, causing wear and tear. The force is greatly increased. When inorganic minerals slide at high speed on the metal surface, their scraping effect is not small. So the speed should not be adjusted too high.
3. The screw rotates in the barrel, and the friction between the material and the two causes the working surface of the screw and the barrel to gradually wear out: the diameter of the screw gradually decreases, and the diameter of the inner hole of the barrel gradually increases. In this way, the cooperation and diameter gap between the screw and the barrel will increase a little bit with the gradual wear of the two. However, since the resistance of the head and the diverter plate in front of the barrel has not changed, this increases the leakage flow when the extruded material advances, that is, the flow of the material from the diameter gap to the feeding direction increases. As a result, the output of plastic machinery has declined. This phenomenon increases the residence time of the material in the barrel, causing the material to decompose. If it is polyvinyl chloride, the hydrogen chloride gas generated by the decomposition strengthens the corrosion of the screw and barrel. .
4. If there are fillers such as calcium carbonate and glass fiber in the material, it can accelerate the wear of the screw and barrel.
5. Because the material is not plasticized evenly, or metal foreign matter is mixed into the material, the torque of the screw suddenly increases, and this torque exceeds the strength limit of the screw, causing the screw to break. This is an unconventional accident damage.
Maintenance precautions:
1. When the screw does not reach the preset temperature, do not start the machine.
2. Prevent metal fragments and sundries from falling into the hopper. If recycled materials are processed, a magnetic hopper is required to prevent iron filings from entering the hopper.
3. When using anti-spill, make sure that the plastic in the material is completely melted, so as not to damage the transmission system parts when the screw is backed up.
4. When using new plastic, the rest of the screw should be cleaned.
5. When the temperature of the molten plastic is normal but the black spots or discoloration of the molten plastic are continuously found, the glue screw should be checked.
6. During processing, try to make the material plasticized evenly, and do not let metal foreign matter mix into the material, so as to reduce the torque of the screw and rotation.
vertical machine tube set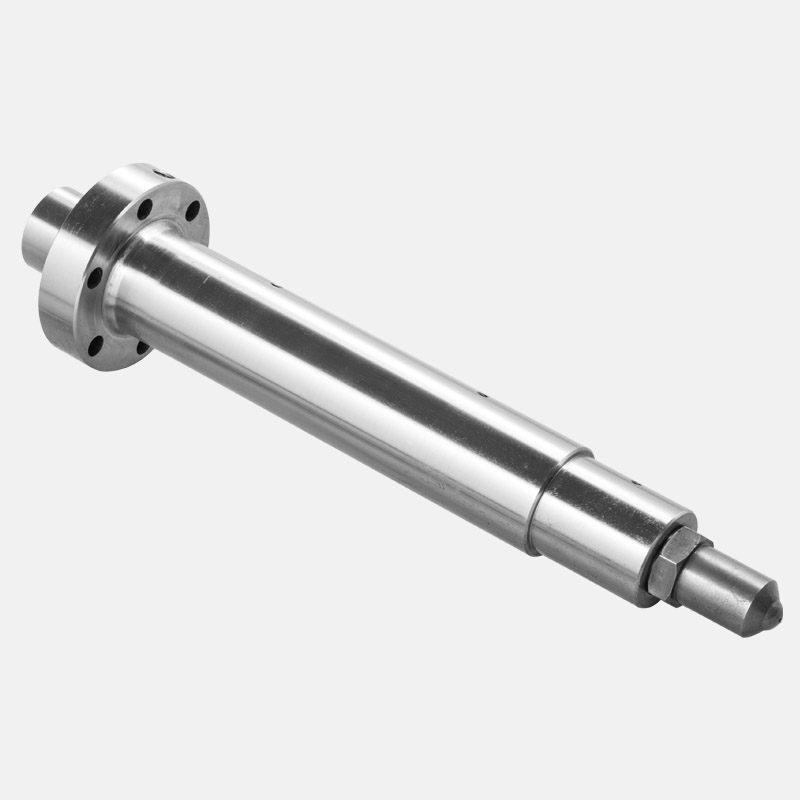