1.Surface Hardening:
The
Nitriding screw barrel process introduces nitrogen into the surface of the screw barrel material, creating a hardened layer. For instance, through gas nitriding, nitrogen reacts with the steel, forming hard nitrides like iron nitride. This outer layer provides a durable surface that resists deformation and wear during the cyclic stresses of extrusion.
2.Increased Wear Resistance:
Nitriding imparts increased wear resistance to the screw barrel surface. For example, in the extrusion of abrasive materials, a nitrided surface can withstand the erosive effects better than untreated surfaces. This wear resistance directly contributes to the fatigue strength by preventing material loss and maintaining the structural integrity of the screw barrel.
3.Formation of Nitrided Case:
Nitriding creates a nitrided case, often a few micrometers thick, on the outer layer of the screw barrel material. This case is typically composed of hard nitrides such as iron nitride. The formation of this nitrided case acts as a protective barrier, minimizing the impact of abrasive wear during extrusion processes.
4.Resistance to Fretting Wear:
Nitriding mitigates fretting wear by forming a wear-resistant surface. In applications where the screw barrel experiences oscillatory movements, as seen in some extrusion processes, a nitrided surface reduces the fretting wear and the associated stress, thus contributing to the fatigue strength.
5.Retained Toughness in the Core:
While the surface is hardened, the core of the material maintains its toughness. This is exemplified in situations where the screw barrel encounters sudden stress, such as during material surges in extrusion. The combination of a hard surface and tough core prevents brittle fracture and ensures the screw barrel's fatigue resistance.
6.Reduction in Microcracks and Stress Concentrators:
Nitriding reduces the occurrence of microcracks and stress concentrators on the surface. In contrast to untreated surfaces that may develop microcracks, a nitrided surface exhibits improved resistance. This reduction in stress concentrators is vital for preventing the initiation and propagation of cracks during cyclic loading.
7.Improved Endurance Limit:
Nitriding contributes to an increased endurance limit, exemplified by the screw barrel's ability to endure a higher number of loading cycles before failure. In extrusion applications with varying loads, the improved endurance limit ensures the screw barrel's longevity and reliability in continuous production.
8.Resistance to Corrosion Fatigue:
Nitrided surfaces exhibit resistance to corrosion, which is crucial in environments where corrosion fatigue is a concern. For instance, in extrusion processes involving corrosive materials or exposure to harsh conditions, nitriding prevents corrosion-related degradation, enhancing the screw barrel's overall fatigue resistance.
9.Enhanced Thermal Stability:
Nitriding contributes to improved thermal stability by altering the material's microstructure. This is particularly beneficial in extrusion processes with temperature variations. The enhanced thermal stability ensures that the screw barrel maintains its mechanical properties, contributing to fatigue resistance even under challenging thermal conditions.
rubber plunger rod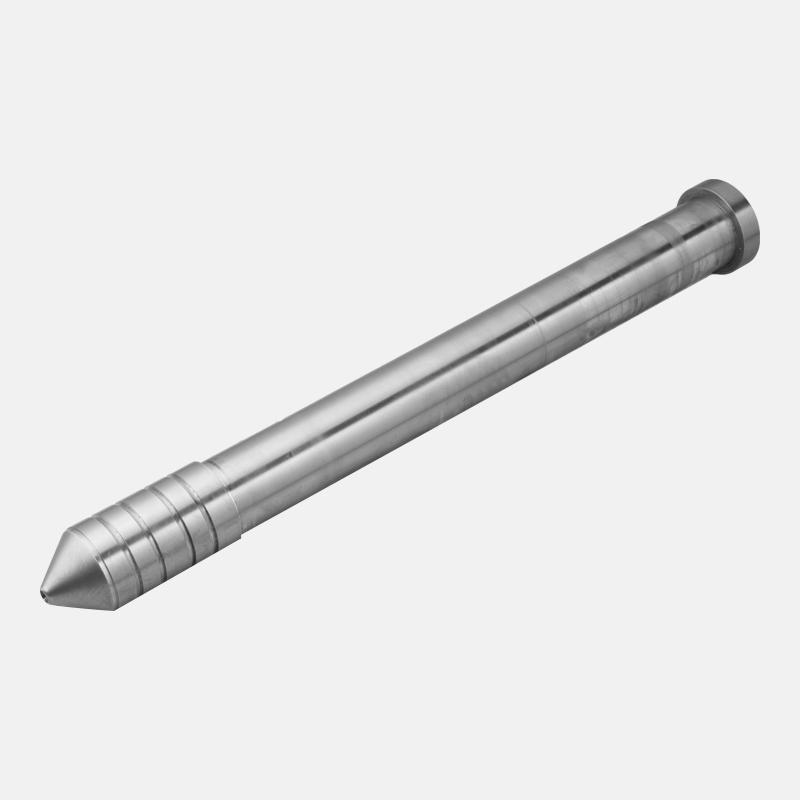